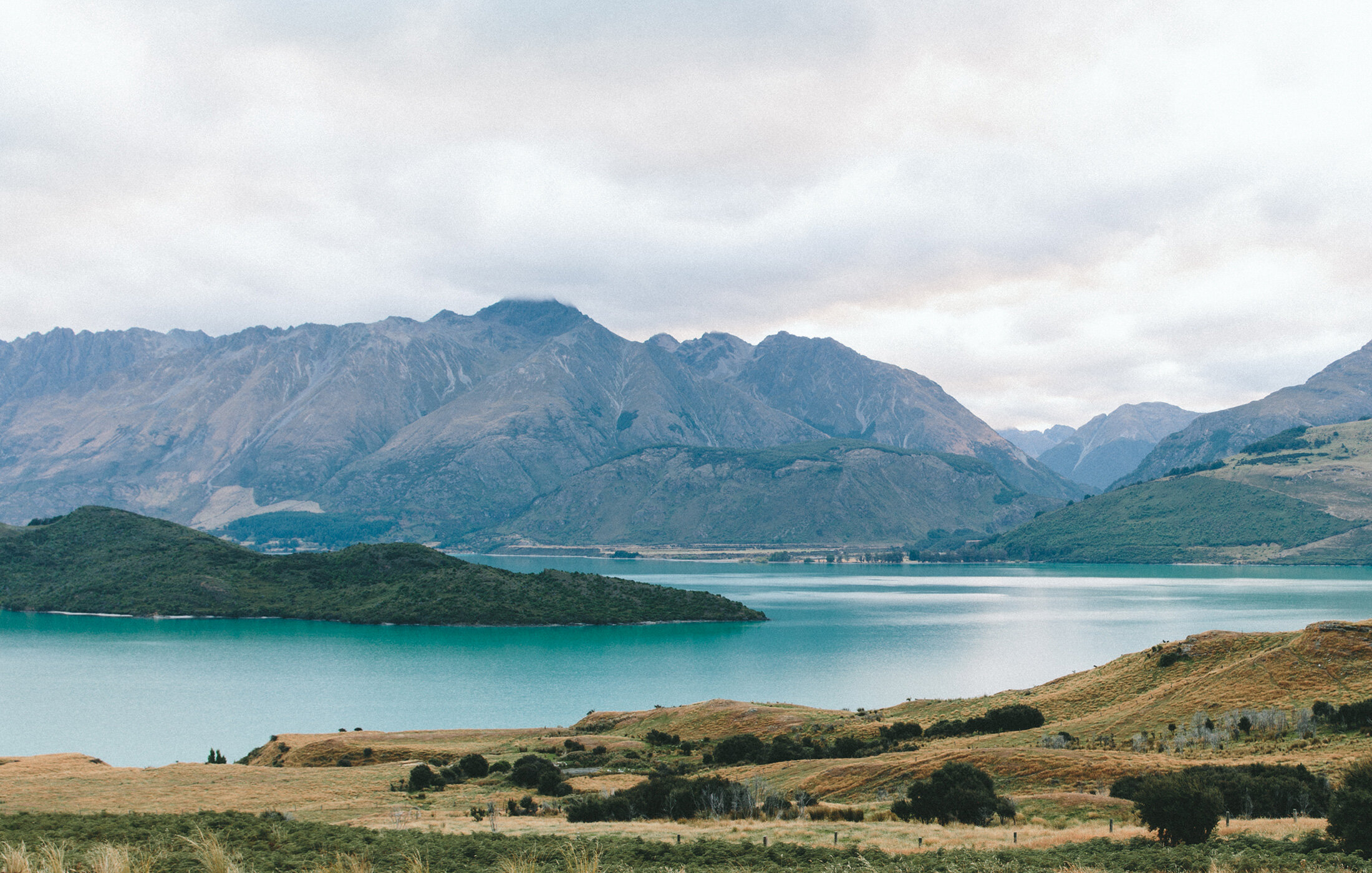
TPU (Thermoplastic Polyurethane) is a flexible, elastic, and durable 3D printing filament widely used for applications requiring elasticity, impact resistance, and wear resistance. It's part of the TPE (Thermoplastic Elastomers) family but is more rigid than some other TPE materials, striking a balance between flexibility and strength.
Properties of TPU Filament
Material Composition: TPU is a polymer blend combining hard plastic (thermoplastic) and rubber (elastomer), resulting in flexible and resilient material.
Shore Hardness: TPU comes in different hardness levels, typically measured using the Shore scale (A or D). Common values range from Shore 85A (very flexible) to Shore 95A (more rigid).
Elasticity: TPU can stretch significantly and return to its original shape without permanent deformation.
Durability: High resistance to abrasion, tearing, and impact.
Chemical Resistance: Resistant to oils, greases, and certain chemicals.
Moisture Sensitivity: Like Nylon, TPU absorbs moisture from the air, affecting print quality if not kept dry.
Advantages of TPU
Flexibility: Ideal for creating parts requiring movement or bending.
Durability: Resistant to wear, impact, and deformation under stress.
Adhesion: Excellent layer bonding, even at low layer heights.
Temperature Resistance: Can withstand moderate heat (softens around 80–100°C, depending on the type).
Versatility: Can produce soft, bendable parts as well as semi-rigid functional components.
Disadvantages of TPU
Printing Challenges: Requires careful tuning of print settings, especially for flexible filaments.
Speed Limitations: Printing speed must be slower due to its flexibility, which can cause jamming in direct-drive or Bowden extruders.
Post-Processing: Difficult to sand or paint compared to rigid filaments.
Moisture Absorption: Needs to be stored in a dry environment to maintain quality.
Common Applications
Wearables: Watch bands, phone cases, and grips.
Seals and Gaskets: Components requiring flexibility and chemical resistance.
Shock Absorbers: Parts designed to absorb impact or vibration.
Footwear Prototypes: Soles and flexible components for shoes.
Functional Prototypes: Hinges, rubber-like grips, and flexible connectors.
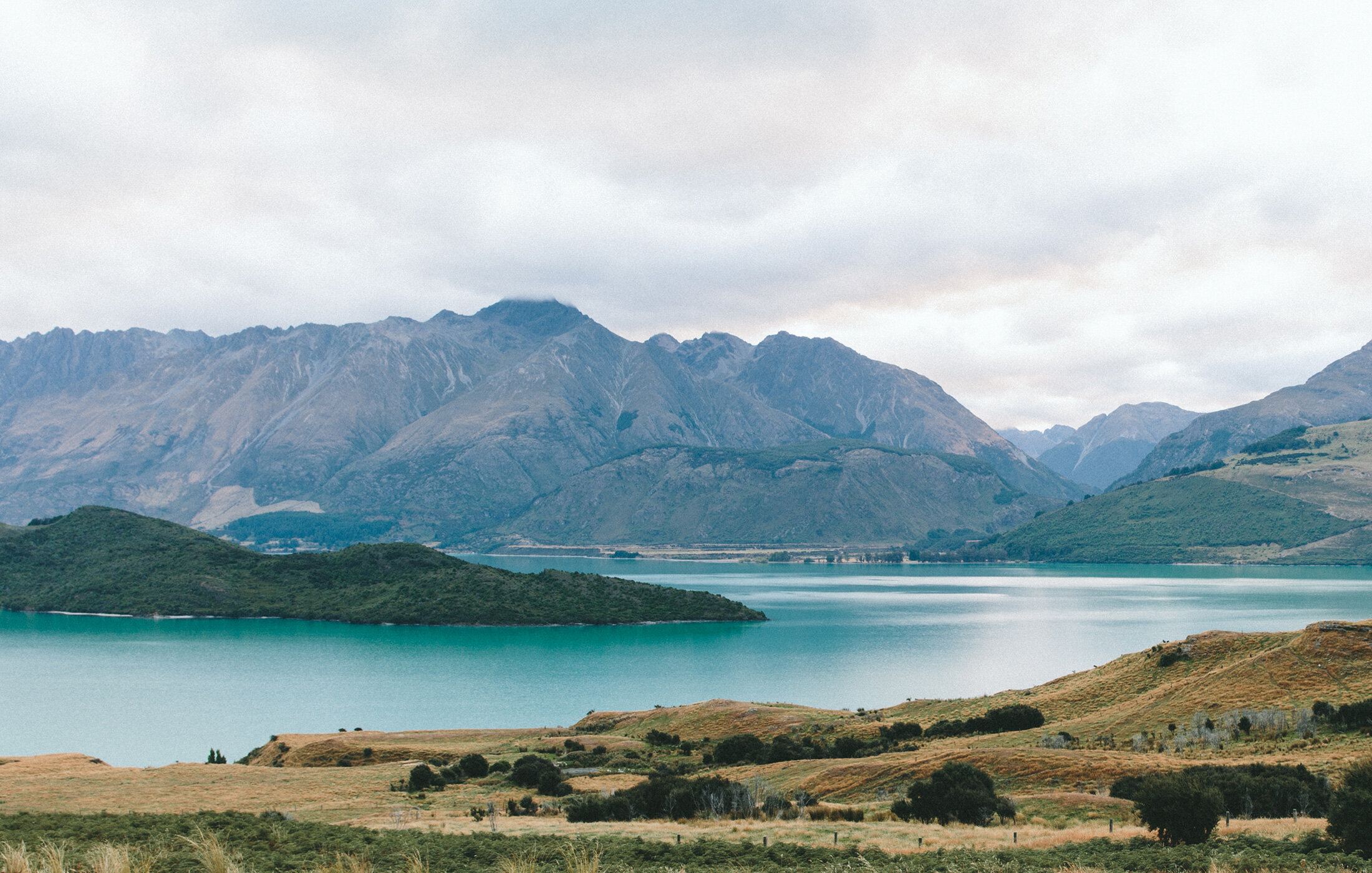
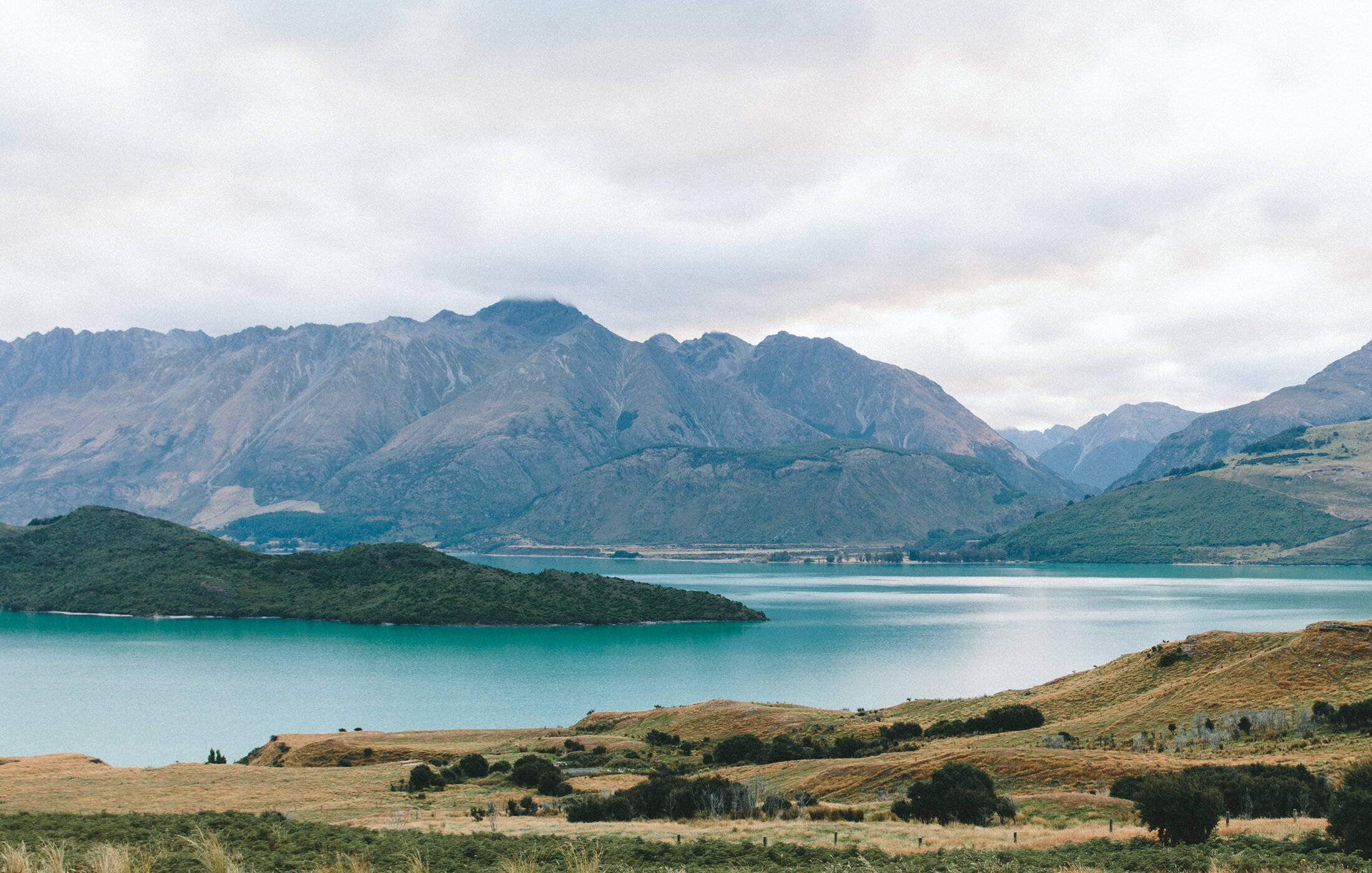
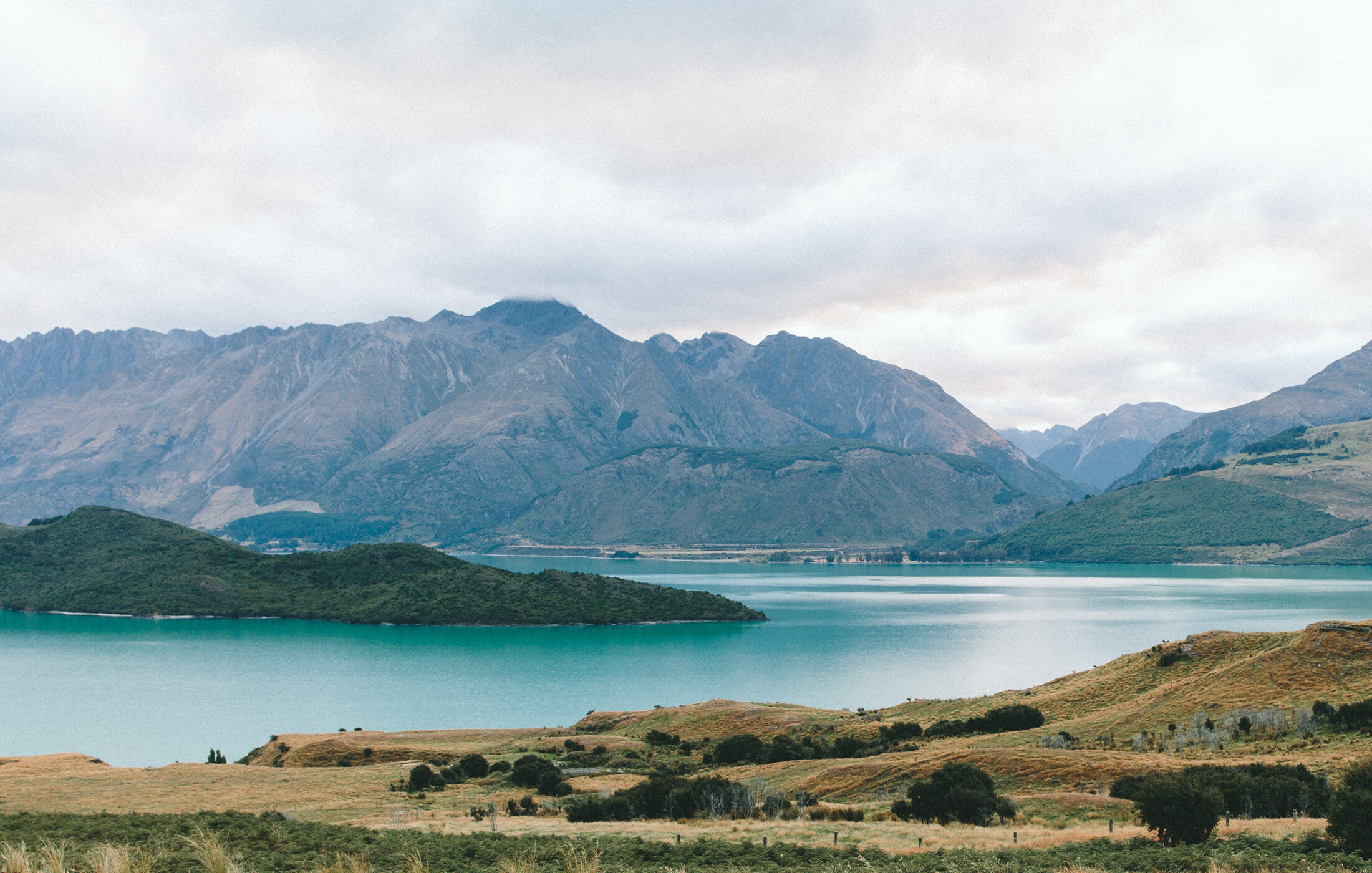
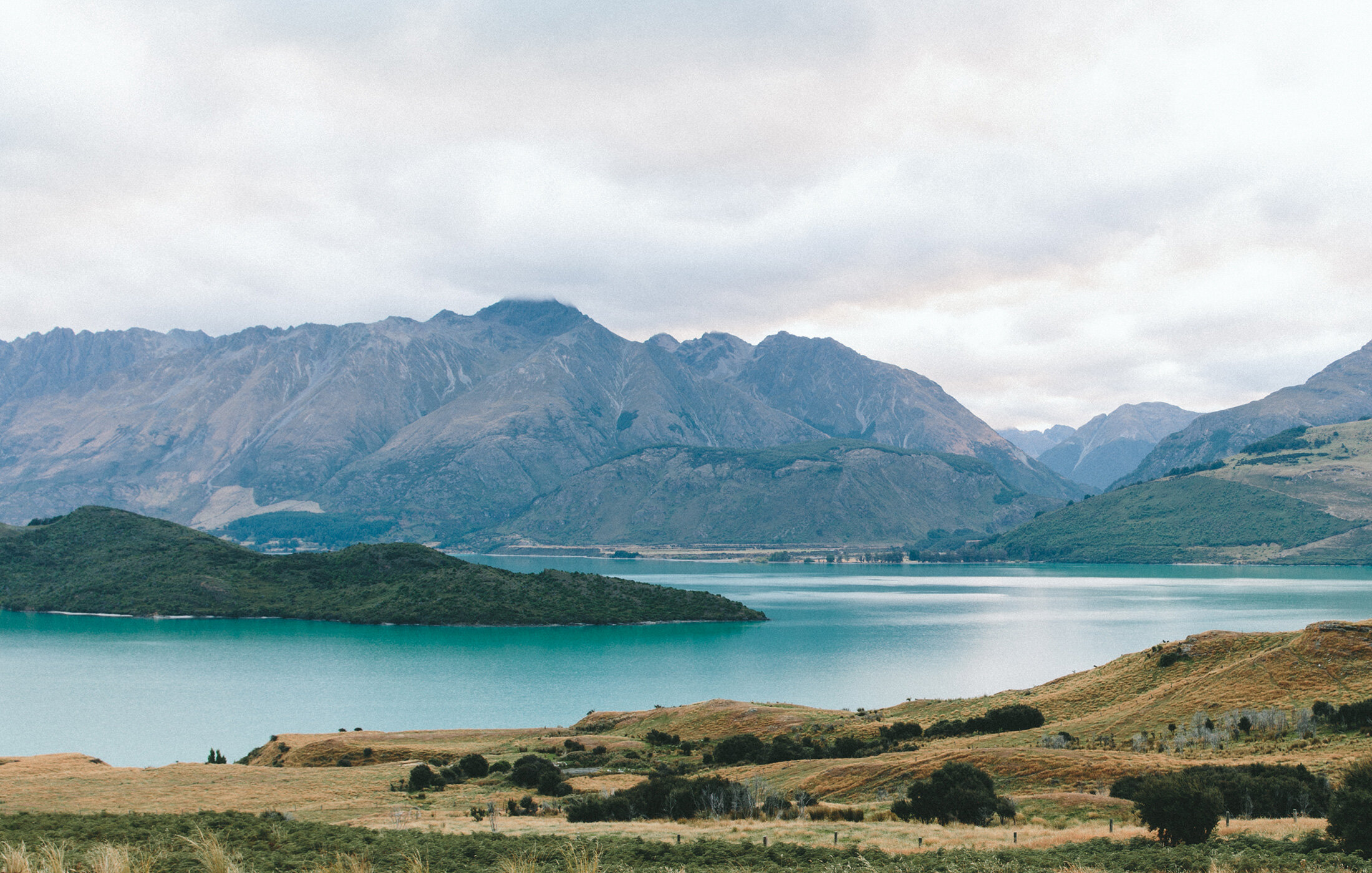
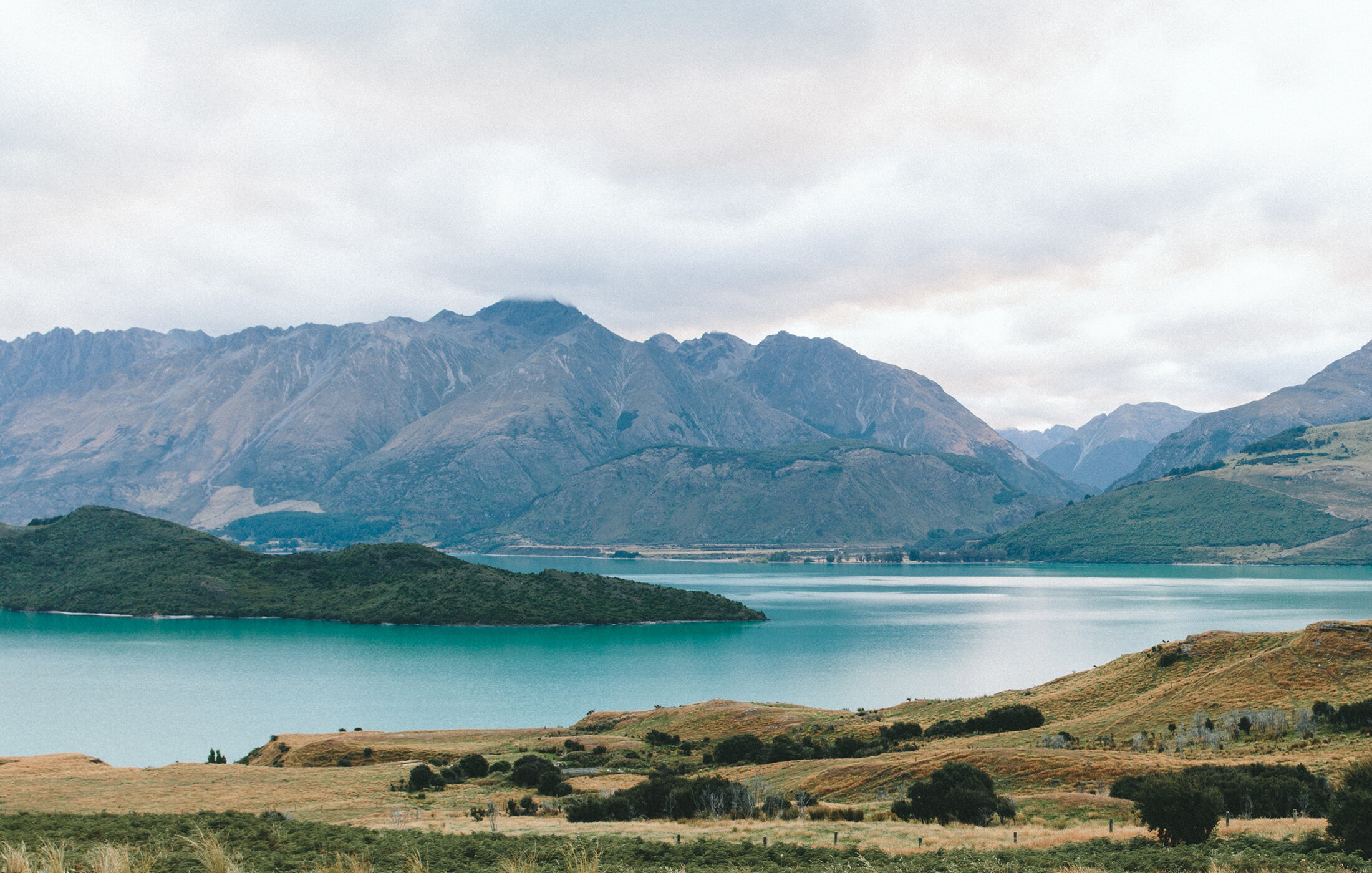
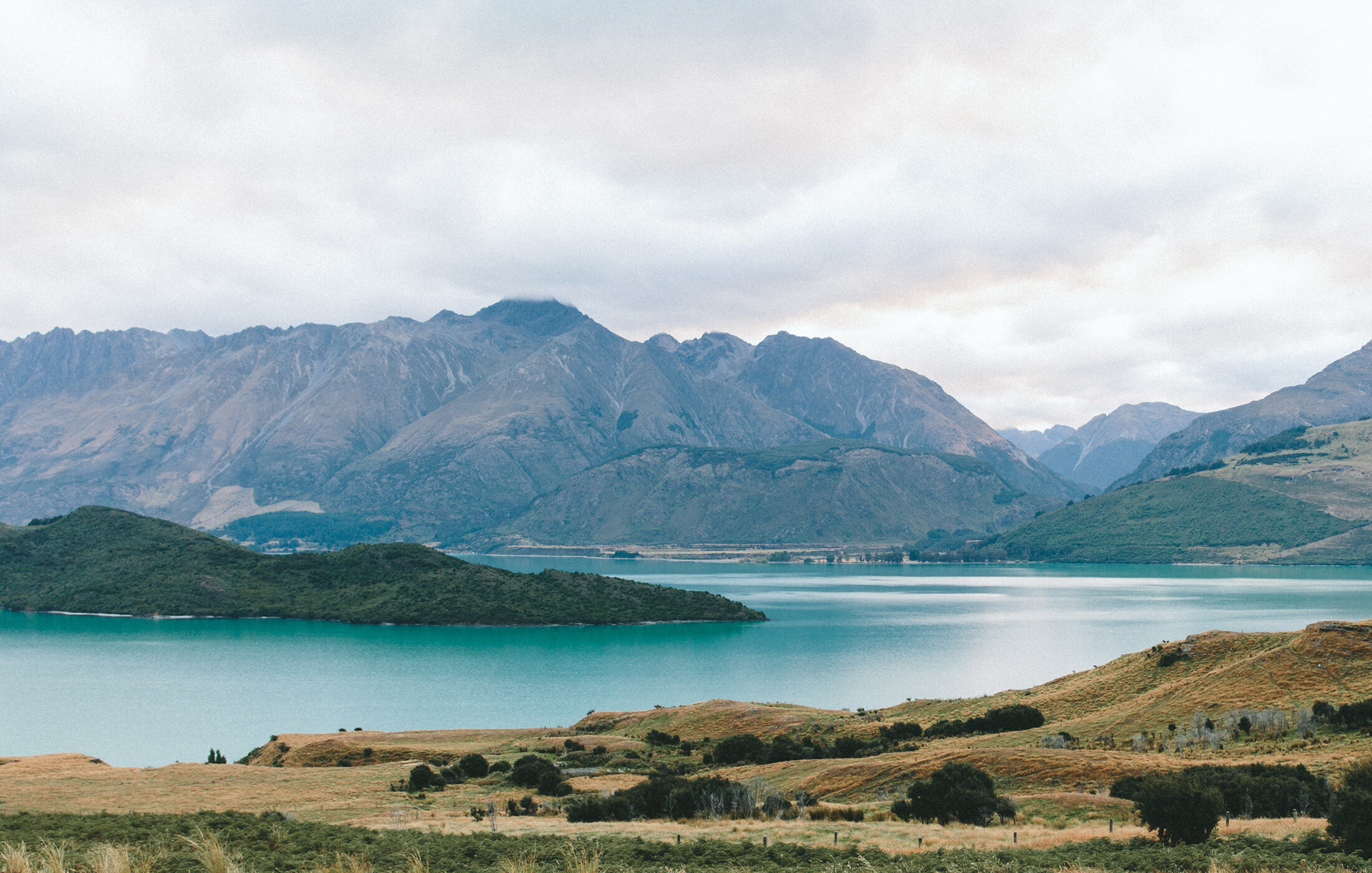